Robotic Naguri
Exploring Robotic Digital Fabrication with Traditional Manual Wood Chiseling
This project centers on a "technology-driven" creative research approach, exploring how robotic digital manufacturing techniques can integrate with traditional manual wood chiseling methods. The aim is to develop highly precise and scalable operational workflows that facilitate opportunities for human-robot collaboration. This research seeks to create a novel chiseling and carving technique for woodworking by applying digital design and robotic manufacturing methods to the field of craftsmanship.
In terms of digital design, the project adopts algorithmic and parametric design methodologies, starting with an analysis of wood grain to develop chisel texture programming capable of defining orderly line patterns. This effort further advances a mechanism for generating repeatable textures. These textural structures serve as the foundation for patterns spanning the material surface, designed to align with the techniques of chiseling.
For robotic digital manufacturing, the project utilizes the Rhino/Grasshopper environment alongside a self-developed TACO KUKA software plugin to construct an integrated industrial robotic arm control framework. Incorporating the concept of a Digital Twin, this framework simulates machining scenarios in a virtual environment, enabling the design and optimization of robotic workflows. Through bidirectional iterations between digital simulation and physical manufacturing, parameters are adjusted and robotic movements refined to achieve continuous improvement and optimization.
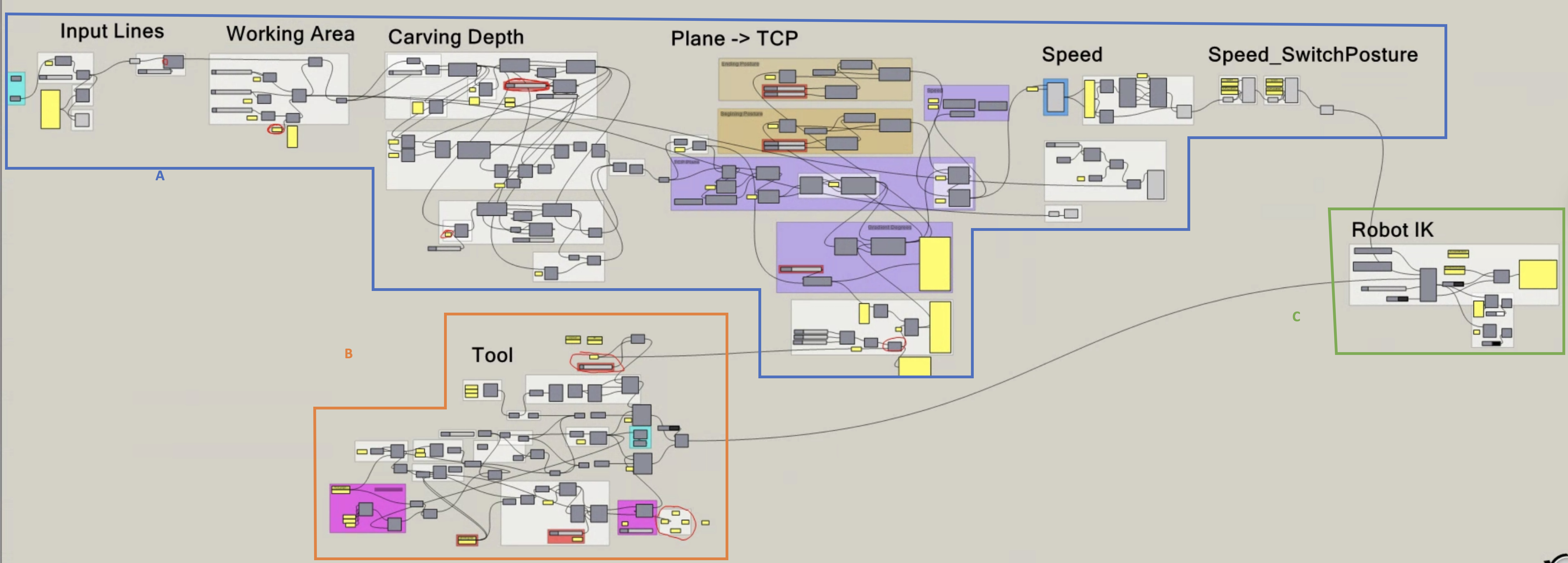
Ultimately, this project aims to develop a digital manufacturing process tailored for wood chiseling craftsmanship. By merging physical and virtual environments, it seeks to realize innovative techniques and explore advanced models of human-robot collaborative craftsmanship.
Artist/Director: Scottie Chih-Chieh Huang
BioLogicDesign Team: Deng-Feng Jiang, Jie-Ke Pan, Yi-Hua Ho
Collaborator: Shih-Yuan Wang (Robotic Tech Developer)
---
本計畫以「技術性導向」的創作研究為核心,探索機器人數位製造技術如何結合傳統手工木工鑿刀技法,開發出具高度精密度且可大量執行的作業流程,藉此促進人機協作的可能性。本研究旨在創造一種新型態的木工鑿刀雕刻技藝,將數位設計與機械手臂的數位製造方法應用於工藝領域。
在數位設計方面,計畫採用演算法與參數設計方法,從木紋的分析出發,設計出能定義線條秩序的鑿刀紋理編程,進一步發展出可重複生成的紋路機制。這些紋理結構以遍佈材料的整體紋路為基礎,產生符合鑿刀技法排列的路徑。
在機械手臂數位製造上,計畫運用Rhino/Grasshopper環境及自行開發的TACO KUKA軟體外掛,構建一個整體的工業機械手臂控制架構。此架構結合數位孿生(Digital Twin)的概念,於虛擬環境中模擬加工場景,進而設計並優化機械手臂的作業流程。透過數位模擬與實體製造的雙向迭代,調整參數並改進手臂運動方式,以達成改良和優化的目標。
最終,本計畫開發一套適用於木材鑿刀工藝的數位製造流程,將實體與虛擬環境結合,發展「順紋生長」、「異紋擾動 」兩件梧桐木成品,以此示範人機協作在工藝領域的作業模式,以及數位化鑿刀雕刻技法的可行性
All images and videos courtesy Scottie Chih-Chieh Huang and The BioLogicDesign Lab.